Tampa, FL
The Tampa International Airport has developed a permanent site for portable paving plants on the airport property. Ajax Paving Inc. is the first plant to use this site for a 33,000 yard taxi way extension. The project called for flexural strengths of 725 psi with an air content of 4.5%. To assist in overcoming aggregate challenges Ajax elected to use OptiFlo® 500 at a 5 oz./ cwt. This dosage also assisted in set control.
Premiere provided a self contained EPA friendly admixture trailer for use onsite. The trailer is comprised of six 1000 gallon tanks with quick connect hose fittings and amphonal computer connections. A camera and monitor are also provided to ensure accurate dosing.
“The Tampa airport project has gone quite well. We have experienced consistent air contents and strength throughout the project. Premiere Concrete Admixtures was very responsive to our needs in finding the right admixture to fit with the local materials. The Admixture trailer Premiere supplied was designed to meet all our needs; it incorporates self containment and is capable of quick tear down and set up. Each trailer is interchangeable with all our plants enhancing our flexibility. Premiere’s attention to service and product quality helps ensure our projects success.”
Paul Selesky, Vice President Concrete Operations – Ajax Paving
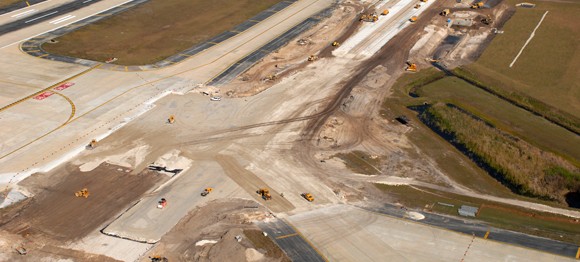
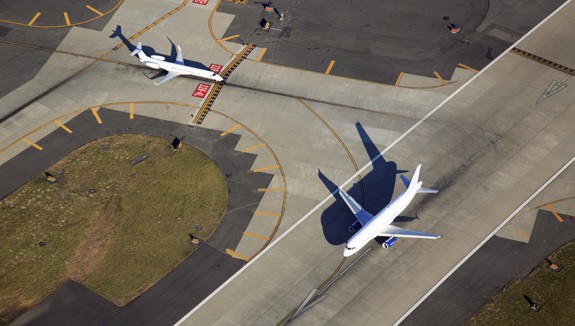