Detroit, MI
For decades, the iconic J.L. Hudson’s flagship store occupied the entire 1200 block of Woodward Avenue and stood as the tallest department store/retail building in the world. Although the building no longer stands, the site’s legacy is still alive and vibrant. In 2017, a mixed-use development broke ground in it’s place. Once complete, it will encompass over 1,400,000 square feet and reach 680 feet into Detroit’s skyline.
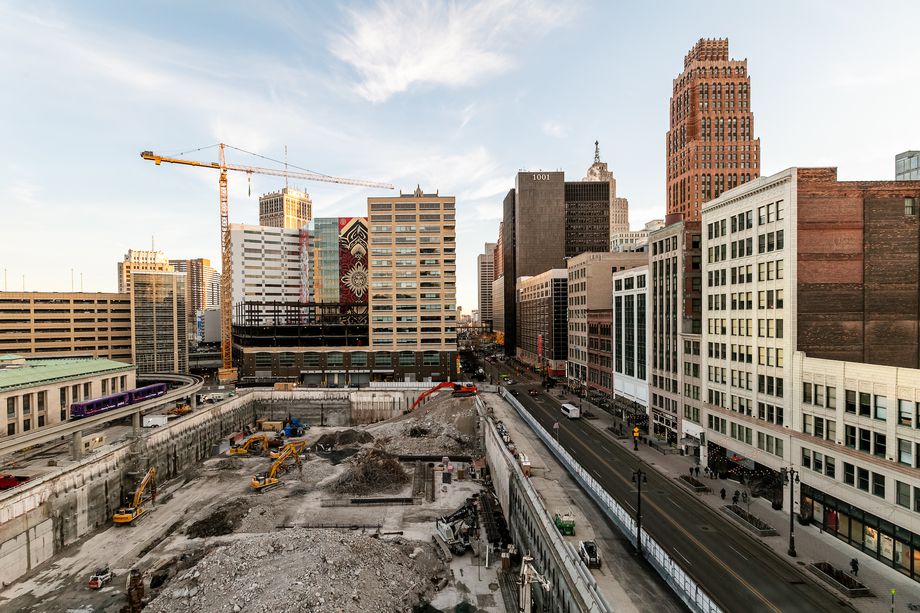
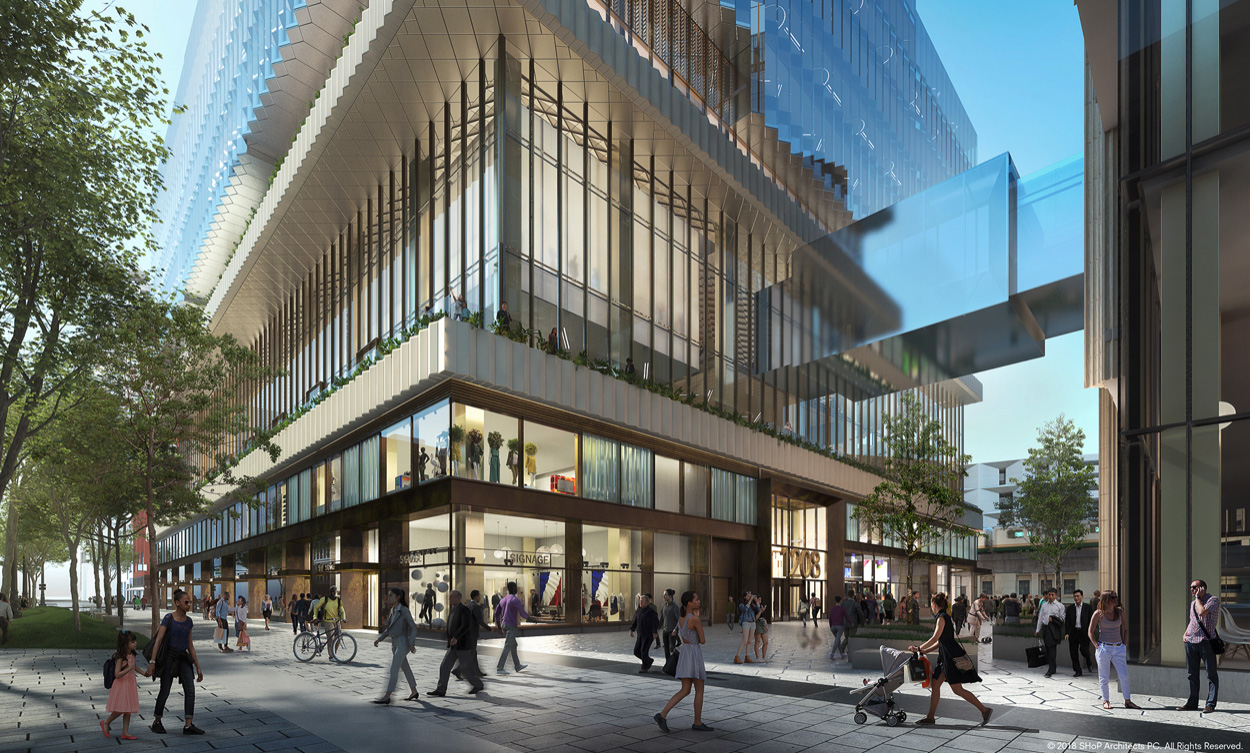
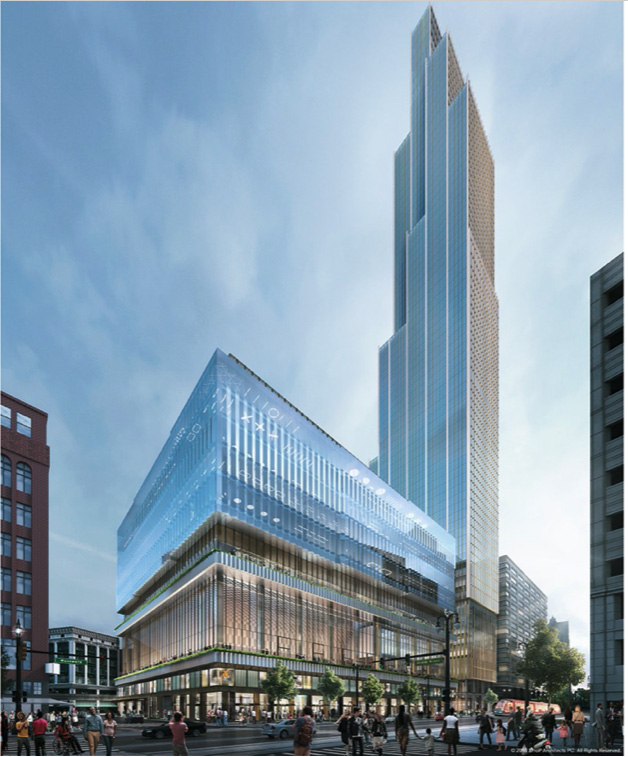